Engine noise and rack and pinion noise has decreased significantly over the years due to increasingly stringent regulations on vehicle noise. And this trend has increased with the rise of electric and hybrid vehicles, modern quiet hybrid fuel vehicles, and one-touch start engines. This has a huge positive impact on the surrounding environment, and the stronger noise levels can put pressure on the road. It’s also good news for drivers who want to drive quietly. However, it becomes particularly noticeable when there is a slight noise, a creak, in a quiet engine.
Improvements in road conditions and tire and suspension technology mean that the driving experience becomes smoother and that automotive systems become more pronounced for driving comfort. This further requires the brand influence of car parts with a high-quality guarantee. Automakers need to have confidence that the parts they buy will deliver on their promises. When engineers take the time to fully understand the challenges faced by customers, they can provide effective solutions.
Through thorough testing and exhaustive research, Saint-Gobain’s automotive noise reduction experts have shown that two important characteristics that affect the quality of steering systems are noise and steering experience, respectively.
As shown in Figure 1, the steering rack bearing (also known as the steering rack guide bearing) has a key role in the steering system. The rack bearing is used to ensure continuous engagement between the rack and pinion teeth. If the gear is disengaged from the rack, the entire steering system will not work. The rack bearing is usually attached to the rack by a spring force of 300N.
Figure 1: Schematic diagram of the steering rack, with the sliding layer of the rack bearing shown in red. An example of a rack bearing is shown in the upper left
The forces applied to the rack bearings create friction on the steering rack that affects the steering experience. Therefore, it is important to ensure that the sliding layer of the rack bearing is well designed. Typically, a rack bearing consists of a metal liner layer and a polytetrafluoroethylene (PTFE) layer. The typical design of the rack bearing shape results in a linear contact between the sliding layer of the rack bearing and the steering rack. This creates high pressure on the sliding surface, which in turn increases wear. As the material continues to wear, a gap develops between the teeth of the rack and pinion. This gap can lead to “tooth vibration” or a rattling sound.
A rack bearing that is tailored to individual customer needs and specifications is more likely to ensure a high-quality product throughout the life of the vehicle. Figure 2 gives another example of a finite element analysis of bearing pressure generated by two rack bearing shapes, one of which is less consistent with the rack that provides linear contact and the other is more consistent with the rack, thus providing more contact. The shape with the greater contact reduces the pressure and therefore the wear on the part, so there is less chatter in the steering system.
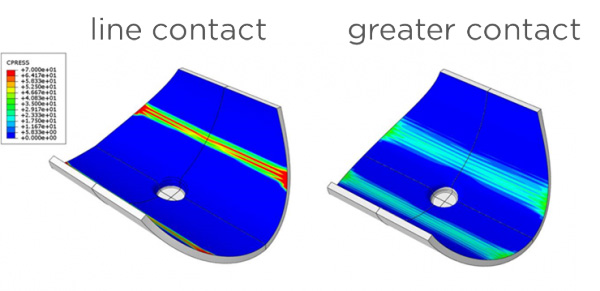
Figure 2: FEA pressure analysis of 1kN applied by the rack shaft on two rack-bearing shapes as shown in Figure 3: the left is a linear contact; the right is a larger contact.
Another problem with high wear rates is the increase in friction over time. Bearings made of sintered bronze and PTFE typically have a thin PTFE layer, and once worn, the bronze layer is exposed to the steering rack. In other words, increasing the friction of the system.
Bearings with larger contact, on the other hand, have a lower wear rate and ensure that the metal part of the structure is not exposed. Figure 3 shows the effect of durability testing on the friction and static and dynamic friction values for the sintered bronze and PTFE products, both of which have a line contact design, and the two Saint-Gobain NORGLIDE rack bearings, which have a larger contact design. The sintered bronze and PTFE bearings show a significant and continuous increase in friction values throughout the life of the part, but the NORGLIDE solution maintains consistent friction and static and dynamic friction values.
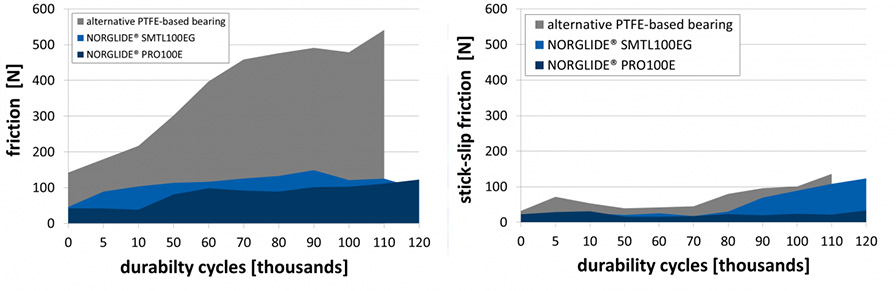
Figure 3: With the durability test, we can see the effect of wear on performance. The actual (a) dynamic friction and (b) static and dynamic friction tests pass.
[1] Danijela Miloradovi, Jasna Gli ovi, Jovanka Luki, “Road vehicle noise regulations – trends and future activities”, Mobility and Vehicle Mechanics, vol. 43, no. 1, 2017
(We do not share your data with anybody, and only use it for its intended purpose)
The Previous Articles:
What Is Rack and Pinion Bushing? How To Tell If Rack and Pinion Bushings Are Bad?
Why Steering Rack Makes Noise When Turning?
How To Rebuild A Steering Rack?
What Is A Rotary Valve Power Steering Rack?
Rack And Pinion System Vs Power Steering System: What Are The Differences?
Power Steering Rack Market Analysis Report (Japan Market)
What Causes Steering Rack to Go Bad?
Design Of Car Rack And Pinion Steering Racks
What Is The Intelligent Steering Rack Used By VW, Toyota, Honda And Renault?
Leave A Comment