In many articles on automotive websites, there is an opinion that a turn of lock in total will hurt the steering machine. Some drivers will tell you that when a turn of lock in total, the pressure inside the steering system will be so high that it will break the steering pump. So a turn of lock in total will really hurt the steering rack? Does it have any effect on the steering system or not? Today we will talk about this topic!
The mechanism used to change the direction of travel in a car is called the steering system. The function of the steering system is to ensure that the car can drive straight or steer according to the driver's will. The steering system can be divided into two types: mechanical steering system and power steering system, and the power steering system is formed by adding a set of steering power devices to the mechanical steering system. There are three kinds of power steering systems: mechanical hydraulic power steering, electro-hydraulic power steering, and electric power steering. The following is an analysis of how the steering system will react after a turn of lock in total.
The mechanical steering system uses the driver's physical strength as the steering energy, and all the components that transmit the force are mechanical, mainly consisting of three major parts: steering manipulator, steering gear, and steering transmission mechanism. The common ones are rack and pinion type, worm crank pin type, and recirculating ball type. These steering machines have internal mechanical limiting devices when the steering wheel is killed in the position, and some models also have a limiting screw on the steering wheel, which directly limits the steering limit position. So this kind of steering system has no effect on the steering machine when a turn of lock in total. However, this steering system is rare and only used in some very low-end models.
Mechanical hydraulic power assist is a common type of power assist, referred to as HPS, with mature and reliable technology and low cost. This type of assistance is part of the engine power output into hydraulic pump pressure, the steering system to apply auxiliary force so that the tired steering.
Its working principle is that when the steering wheel is not turned, the pressure inside the chamber on both sides of the piston is the same and in a balanced state. When the steering wheel is turned, the mechanical control valve connected to the steering column will be opened or closed accordingly, one side of the fluid no longer through the hydraulic cylinder and directly back to the reservoir, the other side of the fluid continues to be injected into the hydraulic cylinder, the piston on both sides of the pressure difference, it will be pushed under the action of the hydraulic force, and then produce auxiliary force, at this time we will feel that turning the steering wheel is not so laborious. The different ways of fluid flow in the system can be divided into normal pressure hydraulic power and normal flow hydraulic power. Now, most hydraulic steering power systems are using the normal flow type, the steering pumps commonly use a vane pump.
In the mechanical hydraulic power steering system, the amount of power assist is only related to the speed of steering wheel rotation, which increases with the speed of steering wheel rotation, but not with the steering angle. In other words, the power is only provided when the steering wheel is turning. When a turn of lock in total, because there is no angular speed, there is no need for power, at this time the steering pump unload idle, generally at this time can hear the steering pump “squeak squeak” unload sound. At the same time, in order to prevent excessive rotational torque damage to the pump, each hydraulic system must be equipped with a safety valve to limit the maximum pressure (not only on the steering pump but also on the steering machine). So the mechanical hydraulic power steering system will not damage the steering pump by a turn of lock in total.
Electro-hydraulic power assist is called EHPS for short. The steering oil pump of this system is no longer driven by the engine directly, but by the electric motor, and an electronic control system is added on top of it so that the size of the steering assist force is not only related to the steering angle but also related to the vehicle speed. The speed sensor monitors the speed of the vehicle, and the electronic control unit obtains the data and changes the fluid pressure by controlling the opening degree of the steering control valve, thus realizing the adjustment of the steering assist force, and realizing the speed-assisted steering, i.e. the assist force increases when driving at low speed, and the driver can operate lightly and flexibly. At high speed, the power of the system decreases, and the driver’s required steering force increases, making the driving more stable.
The structure and working principle of the electro-hydraulic power steering system and mechanical hydraulic power steering system are basically the same, the difference only lies in the different driving modes of steering pump and steering with speed. In this kind of steering system, when the steering wheel is killed, the steering pump unloads and idles. The maximum working pressure of the system occurs when the steering wheel is turned rapidly without moving in place, but there is no need to worry about damaging the hydraulic pump by steering too fast in place because the electro-hydraulic power steering system will also be equipped with safety valves. So the electro-hydraulic power steering system will not cause damage to the steering system because the steering pump is damaged by beating the steering wheel to death.
The electric power steering system referred to as EPS, provides direct steering assistance from an electric power unit, eliminating the need for a hydraulic power steering system, such as a power steering oil pump. In addition, it has the features of simple adjustment, and flexible assembly and can provide steering power under various conditions. Therefore, many passenger cars are now using electric power steering systems.
The electric power steering system consists of a steering sensing device, a vehicle speed sensor, a power-assisted mechanical device, a steering-assisted motor, and a microcomputer control unit. It works as follows: the microcomputer control unit determines the size and direction of the steering power according to the signals from the steering sensing device and the vehicle speed sensor and drives the motor to assist the steering operation. When the driver steers the steering wheel, the torque sensor detects the steering wheel and the size of the torque and sends the voltage signal to the electronic control unit. The electronic control unit sends a command to the motor controller according to the torque voltage signal, direction of rotation, and vehicle speed signal detected by the torque sensor so that the motor outputs the corresponding size and direction of the steering power torque to generate auxiliary power. When the car is not steering, the electronic control unit does not send commands to the motor controller, and the motor does not work.
If the electric power steering system continues to steer for a long time, such as side parking, moving the library, etc., the steering motor will overheat and stop working, then the steering power disappears. This is a protection function of the electric power steering system to prevent the steering motor from burning up. When a turn of lock in total, there is no steering angle change signal, but there is a tendency for the car to turn back to positive automatically after steering, and the larger the steering angle is, the more obvious this tendency is. In order to maintain the steering angle, the steering machine will also produce a corresponding force to balance with it, so the steering motor is working at this time. If this process takes too long, the steering motor will heat up to produce thermal protection and stop working. Therefore, the electric power steering system generally does not allow a turn of lock in total and is held for a long time. It is also stipulated in the manual of the car that it is generally prohibited to beat the steering wheel to death for more than 5 seconds.
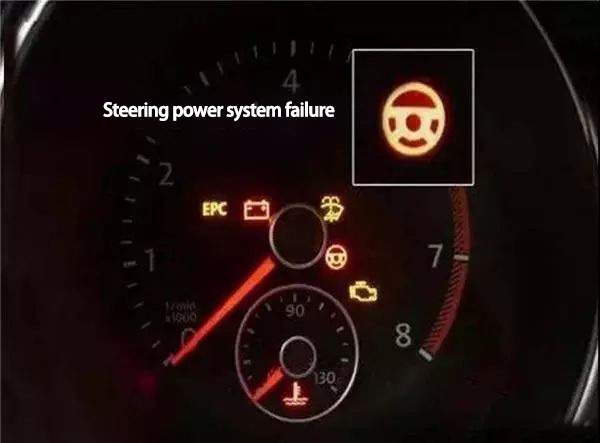
After the above analysis, we can conclude that: for the mechanical steering system, the steering wheel is a turn of lock in total without any effect; for the mechanical hydraulic power steering system and electric hydraulic power steering system, the steering wheel is a turn of lock in total will cause the internal pressure of the system to increase, and the long time high-pressure operation will shorten the life of the system; for the electric power steering system, it is better not to be a turn of lock in total, because this will easily cause the steering motor to overheat and make The power steering system will stop working. But in daily driving, there are many places where you can’t turn over without a turn of lock in total! So the car will be designed to consider some extreme conditions, such as reducing the turning radius to the end of the steering wheel, as long as it is not in such conditions for a long time, is generally no problem.
(We do not share your data with anybody, and only use it for its intended purpose)
The Previous Articles:
What Is Rack and Pinion Bushing? How To Tell If Rack and Pinion Bushings Are Bad?
Why Steering Rack Makes Noise When Turning?
How To Rebuild A Steering Rack?
What Is A Rotary Valve Power Steering Rack?
Rack And Pinion System Vs Power Steering System: What Are The Differences?
Power Steering Rack Market Analysis Report (Japan Market)
What Causes Steering Rack to Go Bad?
Design Of Car Rack And Pinion Steering Racks
What Is The Intelligent Steering Rack Used By VW, Toyota, Honda And Renault?
Leave A Comment